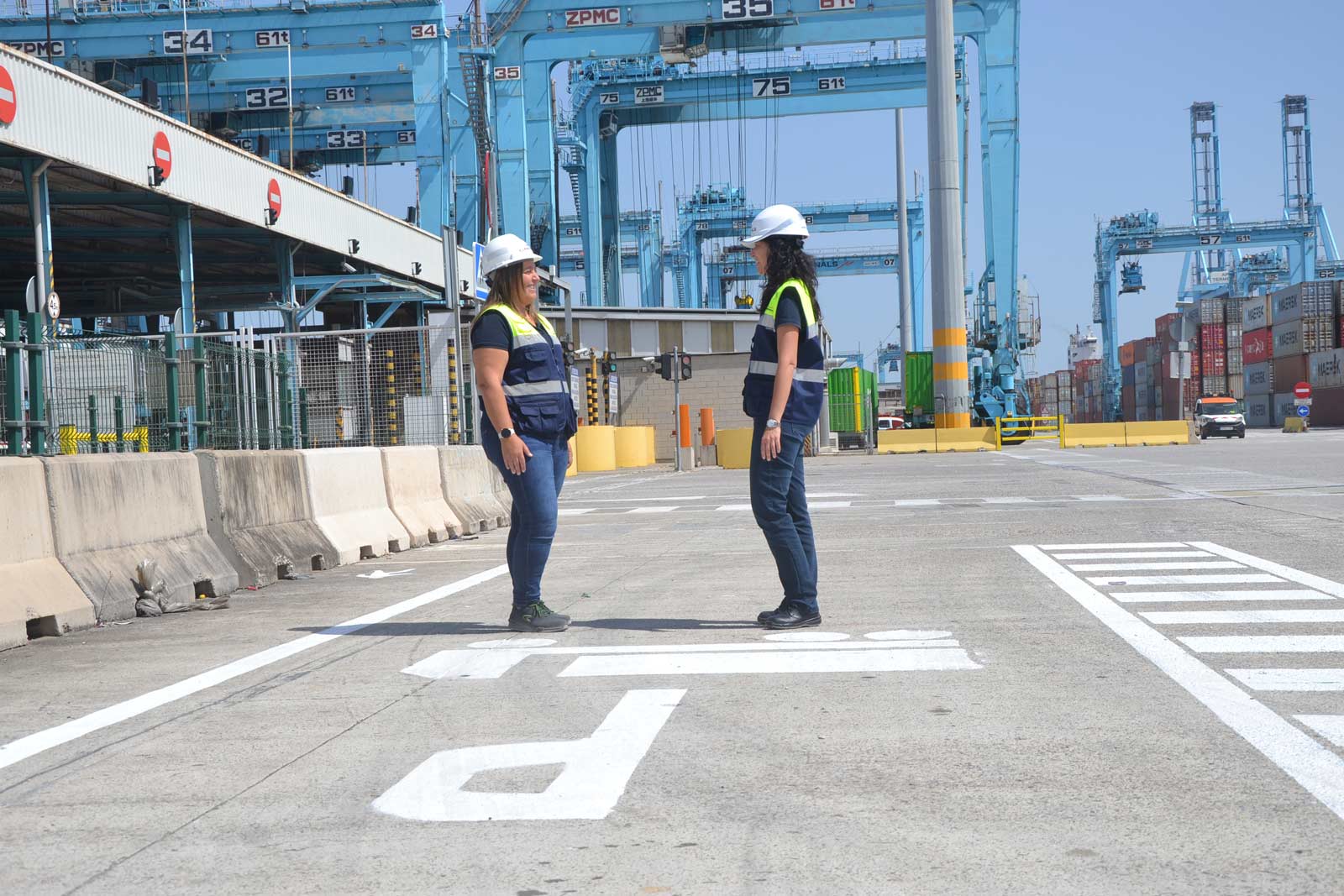
27/05/24
Paint job at APM Terminals Algeciras reduces yard collisions by 50%
When vital safety markings were wearing thin due to the unforgiving Spanish sun, and extreme use by thousands of heavy vehicles, our teammates got to work on finding a solution, collaborating with drivers, paint manufacturers, fellow terminals and safety experts. The result? 50% fewer collisions.
Here, Irene Rodriguez Pina, Engineering, Reliability & Facilities Manager, Asset Maintenance expert at APM Terminals Algeciras explains how they brushed up on safety and reliability, with a lot of thought, and a lick of paint.
- How important are road markings in a terminal environment?
Road markings provide visual guidance to drivers, pedestrians, and other road users, helping them navigate safely through the terminal area. Clear markings delineate lanes, pedestrian crossings, stop points, and other important traffic management features, reducing the risk of accidents and collisions.
- At what point did you realise wear and tear on the markings was an issue?
I would say that the main trigger was that markings were seen as a repetitive contributing factor in several traffic collisions. Insufficient marking was never the main root cause, but it was constantly there, contributing to negative outcomes.
- Who took the initiative to investigate the issue further?
We are part of a global organisation, which brings us a lot of ideas and best practice learnings. So, in this case, we were inspired by Keld Pedersen, Managing Director of APM Terminals West Med, Hubs and Collaboration. He put the focus on safety issues that could be avoided using Lean methodology.
In Algeciras, we have a long trajectory of success applying Lean methodologies to maintenance breakdowns or other safety topics, so it was a natural step to reorient our efforts to specifically traffic collisions. Continuous improvement is our motto.
- Did you contact other terminals within the APM Terminals group to see if this was an issue they shared?
Yes, we contacted several terminals and we performed numerous tests using their recommended paints. However, we realised that our specific type of pavement plus our requirement for faster drying times made the Algeciras setup different. We also contacted Global Functions and we learnt that terminals with the same type of pavement as ours had the same issue with paint.
The issue was known but there was no solution in place at that moment. So, we decided to apply the Lean Safety, Quality, Delivery, Cost (SQDC) approach. No matter the cost no matter the delivery time, first we needed to find a safe solution with the demanded quality for our drivers. Later, we could start focusing on delivery and cost.
- Did you also liaise with manufacturers? Were adaptations needed based on your feedback and findings?
Yes, several manufacturers came to the terminal to understand our needs and later to check the follow-up of the tests. It is not easy to find other examples in which heavy machinery is constantly driving, eroding and dirtying the horizontal signalization. Ports or airports are really exceptional cases in which this situation happens. So it was a long process in which ten different paints were tested on different locations until we reached the current solution.
- Is the paint that is now used more expensive?
If we consider horizontal signalisation costs during one year, that means paint cost plus repainting at the required frequency, we can clearly confirm that we are now saving money.
- Do you have any issues with drivers understanding road markings or instructions? For example, do you use ‘international’ or non-language-specific markings which can be understood no matter where the driver comes from or the language they speak?
Drivers understanding was our most relevant design criteria. The following mandate was repeated in each of our design sessions: “anyone from any company, any country…must understand the road markings”. That was why we dedicated a lot of time to collect Voice of the Customer feedback, gathering the input of many truck and rubber tyred gantry crane (RTG) drivers, before validating any of the proposals we were considering. Based on their feedback, we also did some benchmarking with other ports, airports and with public roads. After that, we designed a new marking layout that was also double checked with our HSSE & Operations teams.
- What has been the impact?
Number of traffic collisions after the implementation of the new road markings with the new high-quality paint have been reduced up to 50%.
We continue to regularly talk to drivers and the common feeling is that we have contributed to create a safer environment. That is the best recognition that we could ever imagine to our efforts. We are proud of this achievement because we can clearly see that marking plays a vital role in promoting safety, efficiency, compliance, and organisation within terminal environments.