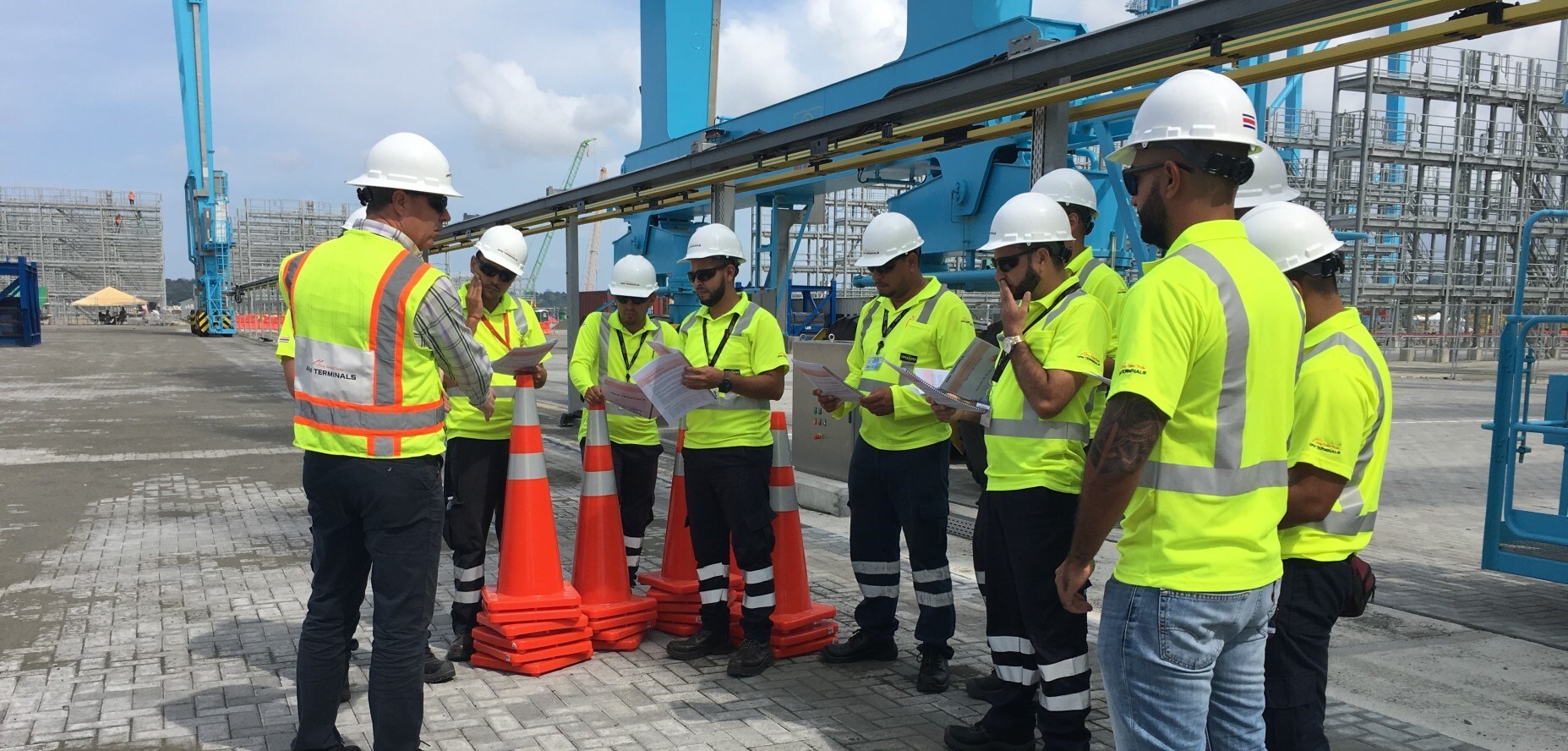
26/09/19
Global standardization increases container terminal efficiency and safety
One year since the implementation of APM Terminal’s new global operator training programme known as ConQuip, and the approach is paying off. The company’s goal is to implement standardized operator training across 38 Global Operations.
This approach allows APM Terminals to share and implement best practice across the organization, reduce costs, and enable smoother operational start-up for new Terminals. One year since the introduction ConQuip and the company is seeing it contribute to improvements in Port Moves Per Hour (PMPH), fewer accidents, and a reduction in skills variance between employees.
Launched as a pilot at APM Terminals Tangier Med Port 2 in August 2018, ConQuip focusses on yard and vessel heavy equipment operations, such as ship to shore and mobile harbour cranes, reach stackers, straddle carriers and rubber tyre gantry. The basis for the training is to initially identify skills gaps.
Skills-gap analysis
Skills gaps are identified using paper-based assessments, on-the-job evaluations and data analysis, carried out on a scheduled and ad hoc basis.
“For example, a ConQuip trainer may notice that a reach stacker operator isn’t consistently picking a container in a single move,” explains Fatima Alvarado, People & Functional Training at APM Terminals. “In such an instance they will be invited to a training.”
This means that each operator receives only the training that he or she requires to raise their skill level. “Instead of a fixed 6-month standard training, regardless of a new operator’s ability and experience, it means that the training can be potentially condensed into a few weeks, with additional training later as we identify further skills gaps,” says Alvarado.
“If you train operators to our global training standards, you reduce accidents, increase performance, engagement and upskill your workforce. Using this approach, we also select operators for training based on their talent and ability to master the equipment.”
In-house trainers
In a significant change to the company’s previous approach to training, all training is now carried out by specially selected in-house trainers at each terminal.
These trainers are equipped with an in-depth knowledge of standardized procedures, and the latest training skills and techniques. They continue to do their job for around 80% and spend 20% of their time training.
“With this approach we can utilise their ‘hands-on’ knowledge as well as developing training skills in-house. It also provides an excellent feedback loop for continuous improvement,” says Alvarado.
Maersk Training as learning partner
In 2018, APM Terminals selected Maersk Training as a learning partner to deploy its operational standards via a Train the Trainer and Effective Training methodology.
Based on APM Terminals standards, Maersk Training have developed the training materials and translated into the local languages. Up to 10 experienced operators (master trainers) at a terminal are trained by a global training team.

Labour force flexibility
Standardising skills across APM Terminals not only ensures that operators are using the best and latest functional skills within the terminal, but also that those skills are transferable between terminals. This provides added labour force flexibility and can ensure that new terminals can be brought up to the same level of operational excellence in the shortest time.
Customer benefits
For customers, it provides consistency of cargo operations at each terminal, wherever it’s located in the world. By improving efficiency and productivity, customers also benefit from shorter vessel working times while APM Terminals frees up additional capacity at the berth.
ConQuip has now been rolled out to more than 12 terminals globally, upskilling more than 1,000 operators.
As awareness of ConQuip increases within these markets it is also helping APM Terminals attract best-in-class Equipment Operators.
“For HR, ConQuip is not just a training program, it’s a great tool in recruitment to make sure we support Operations with qualified employees with right skills, capabilities and attitude who can make a difference in terms of safety and productivity,” concludes Gigi Katsaridze, HR Manager at APM Terminals Poti, Georgia.
APM Terminals Guatemala has had a similar experience, with new candidates selected over the past year according to ConQuip guidelines, already performing at similar levels to experienced operators.
In 2020, we look forward to welcoming all the terminals into our minimum training standards for operators: Conquip.